Power of Smart Maintenance Planning
Proactive maintenance is the key to minimizing downtime and optimizing shopfloor performance. By utilizing modern maintenance planning solutions, manufacturers can leverage the power of machine learning and AI to predict machine failures and plan maintenance tasks accordingly.
Smart maintenance planning is a key driver of shopfloor optimization. By leveraging predictive maintenance, real-time analytics, and efficient scheduling, manufacturers can significantly improve their overall equipment effectiveness.
Here's how it can benefit your operations:
- Real-Time Analytics
Analyze data to optimize maintenance strategies effectively and improve overall availability. By gaining valuable insights into equipment performance and trends, you can make informed decisions and take proactive measures to prevent potential issues. - Simplify Maintenance
Efficiently schedule maintenance and maximize asset utilization using Gantt visualization. This allows you to visualize and plan maintenance tasks, allocate resources effectively, and reduce downtime. - Recurring Downtimes
Keep your machines and equipment running at their best and well-oiled! With a smart maintenance planner, you can establish recurring maintenance schedules, ensuring that regular maintenance tasks are performed to prevent unexpected breakdowns. - Trend Analysis
Identify potential issues on production lines before they lead to costly downtime. By analyzing historical data and trends, the maintenance planner can identify patterns that indicate potential problems, enabling proactive maintenance actions.
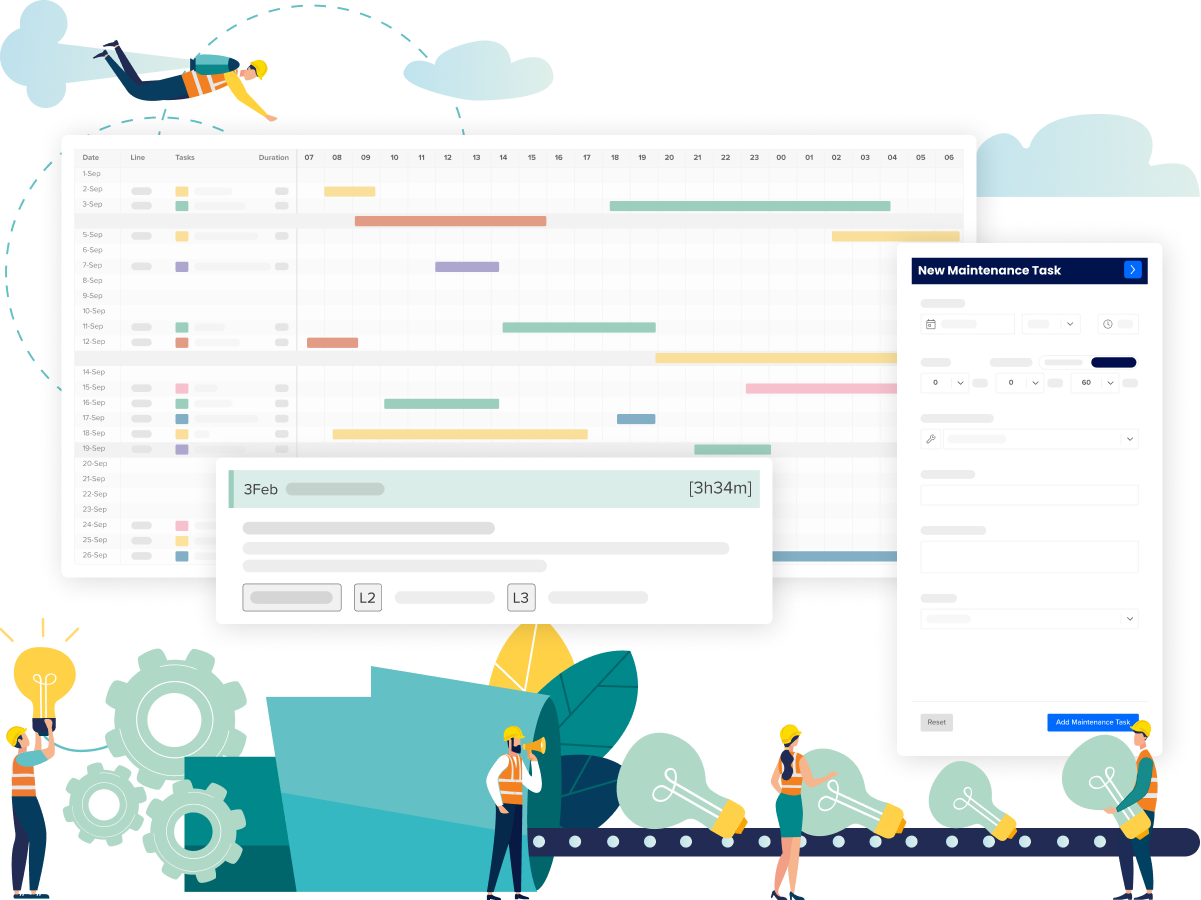
Optimizing Equipment Reliability: Predictive Maintenance Planner MES Enhances Manufacturing Efficiency.
Predictive Maintenance Planner MES
Predictive maintenance takes maintenance planning to the next level by using advanced analytics and machine learning algorithms to predict equipment failures.
Leveraging big data and advanced analytics, a predictive maintenance planner MES empowers manufacturers to proactively schedule maintenance, optimize resources, and monitor machine health in real-time, leading to reduced downtime and improved efficiency.
Here's how a predictive maintenance planner MES can transform your maintenance practices:
Predictive Maintenance
Schedule maintenance proactively with predictive analytics and machine learning to minimize downtime and reduce costs. By analyzing historical data, sensor readings, and machine performance, the planner can identify early warning signs and predict when maintenance is required.
Smart Maintenance Planner
Optimize maintenance resources with our smart factory software and advanced planning to improve efficiency and reduce lead times. By streamlining maintenance processes and optimizing resource allocation, you can achieve better maintenance outcomes while minimizing disruptions to production.
Integrated Machine HealthCheck
Monitor maintenance performance in real-time with customized reports and dashboards to drive asset utilization. With a comprehensive overview of your machine health, you can identify potential issues, track maintenance activities, and make data-driven decisions to optimize your maintenance strategy.
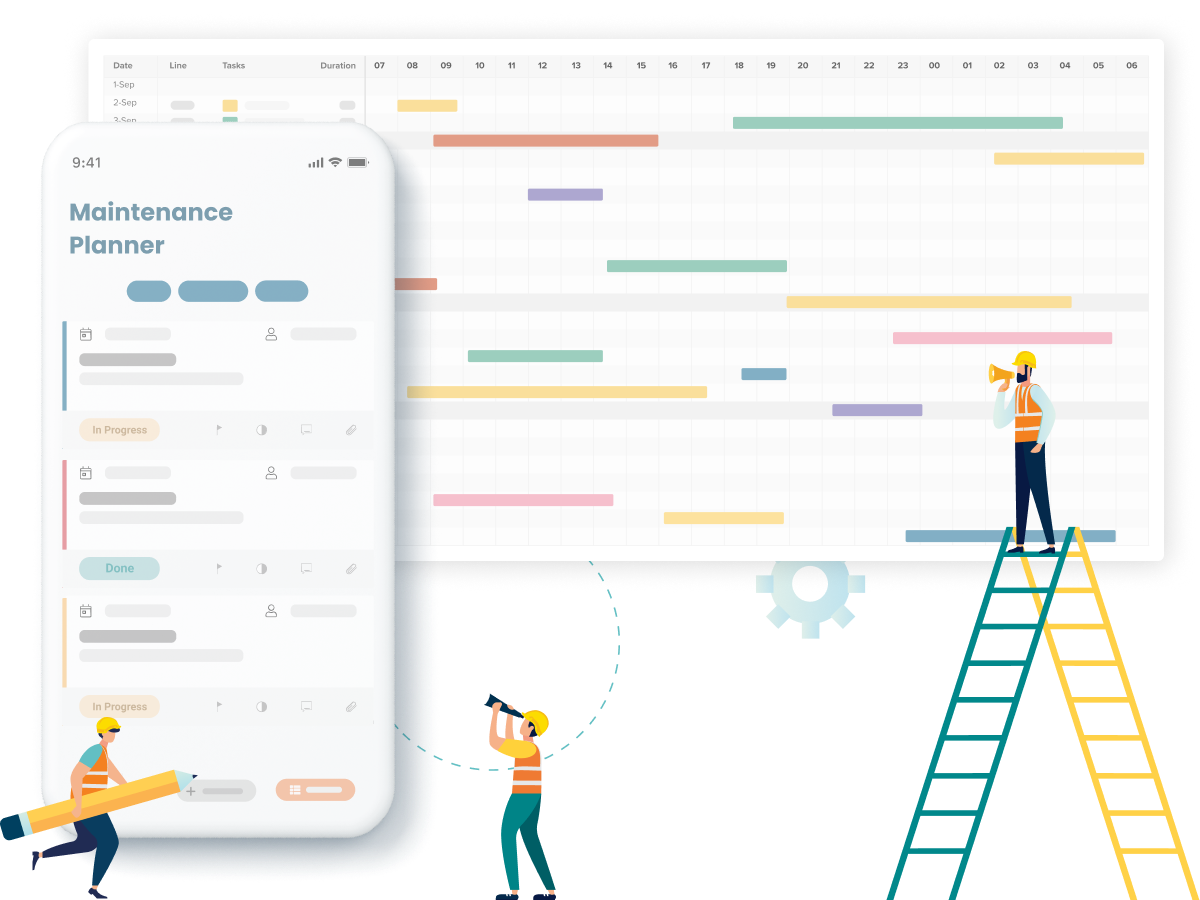
Efficient Synchronization: Streamlining Machine Maintenance with Production Schedules.
Sync Machine Maintenance with Production Schedule
In a fast-paced manufacturing environment, syncing machine maintenance with the production schedule is crucial to avoid disruptions and optimize efficiency.
By synchronizing machine maintenance with the production schedule, manufacturers can minimize disruptions, allocate resources effectively, and optimize overall operational efficiency.
Here's how a smart maintenance planner can help you achieve seamless coordination
Develop a Maintenance Plan
Outline all the maintenance activities that need to be performed, including scheduled and unscheduled tasks. By developing a comprehensive maintenance plan, you can ensure that all necessary maintenance tasks are accounted for.
Schedule Maintenance Tasks
Categorize activities based on their level of criticality to ensure that the most important tasks are completed first. Prioritizing maintenance tasks allows you to allocate resources effectively and minimize unplanned downtime.
Minimize Unplanned Downtimes
Ensure that resources are being utilized optimally and activities are contributing to the overall efficiency of operations. By synchronizing machine maintenance with the production schedule, you can minimize disruptions and maximize productivity.
Preventive Maintenance Planner
Organize Equipment Maintenance with Planner: Maximize Uptime and Minimize Downtime!
Preventive maintenance aims to maximize uptime and minimize downtime by implementing proactive maintenance strategies.
Implementing a preventive maintenance planner allows manufacturers to schedule recurring maintenance, track equipment performance, and establish standard operating procedures, resulting in improved uptime, reduced downtime, and enhanced teamwork.
Here's how a preventive maintenance planner can revolutionize your maintenance processes:
- Plan Recurring Maintenance Once
Save time and improve efficiency by establishing recurring patterns for maintenance tasks, reducing the need for rework and errors. By scheduling recurring maintenance activities in advance, you can ensure that critical maintenance tasks are never overlooked. - Find Mean Time Between Failure
Provides a measure of how often production assets fail by analyzing data on equipment performance, downtime, and maintenance history. By calculating the mean time between failure (MTBF), you can determine the reliability of your assets and schedule maintenance proactively to prevent unexpected breakdowns. - High Mean Time Between Failure
Get solutions to proactively schedule maintenance and minimize downtime to improve the reliability of assets by tracking asset performance. By analyzing asset performance trends and historical data, you can identify opportunities to optimize maintenance intervals and increase asset reliability. - Keep your Team on the same Page
Provides clear guidelines and steps for tasks and processes using Standard Operating Procedures (SOP), which leads to improved teamwork. By standardizing maintenance procedures and ensuring that everyone follows best practices, you can enhance collaboration and streamline maintenance operations.
Increase Resource Utilization
Maximizing resource utilization is a critical aspect of maintenance planning. With a visual management tool, you can prioritize maintenance tasks, optimize resources, and reduce downtime. By achieving optimal efficiency, you can boost profitability and make the most of your available resources.
Standardization Using SOP
Integrating Standard Operating Procedures (SOP) into maintenance planning can streamline tasks and processes, improving efficiency, accuracy, and compliance. By providing clear guidelines and standardized procedures, you can ensure that maintenance activities are performed consistently and to the highest standard.
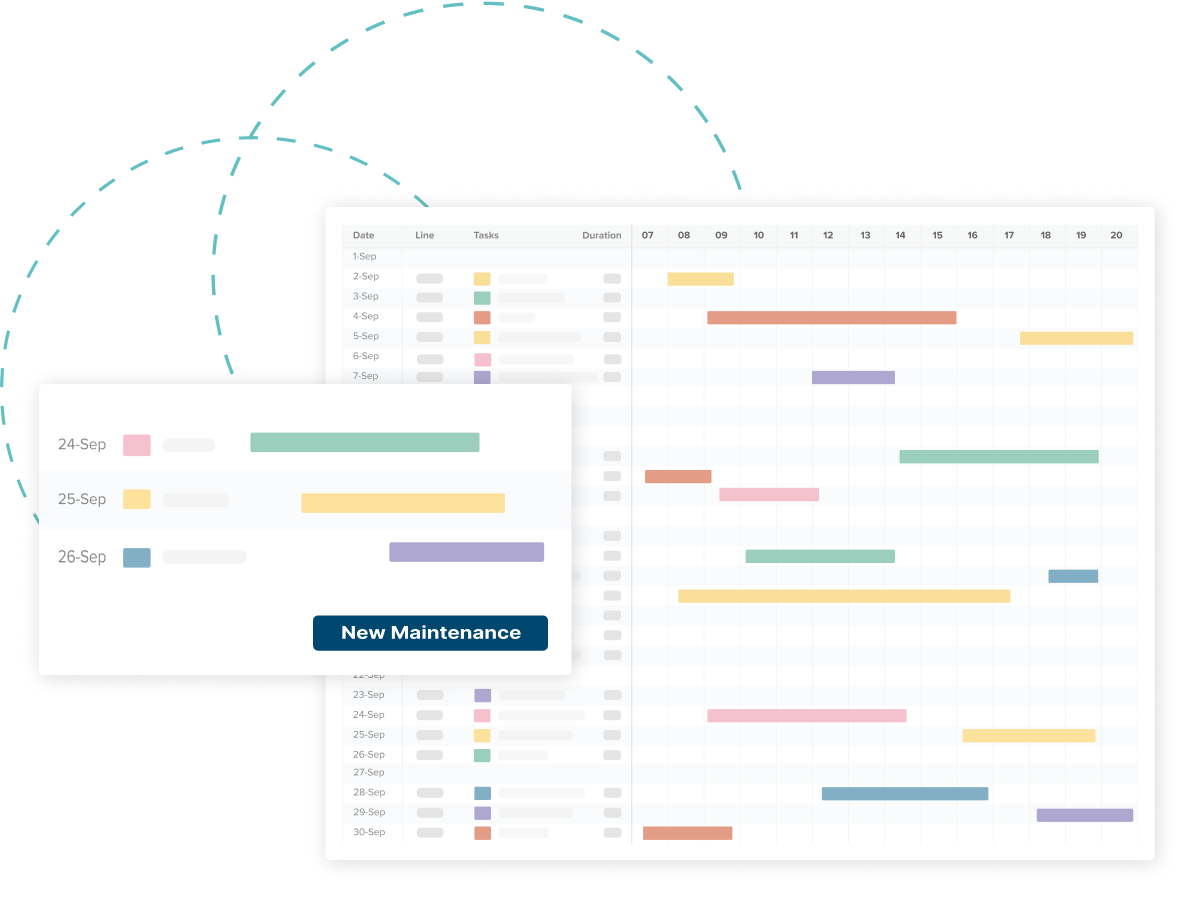
Unlocking Smart Manufacturing: Harnessing the Power of a Smart Maintenance Planner.
Use Smart Maintenance Planner for Smart Manufacturing
In the era of smart manufacturing, optimizing asset performance and reducing downtime are critical for staying competitive. A smart maintenance planner offers a range of features tailored for smart manufacturing
A smart maintenance planner tailored for smart manufacturing empowers manufacturers to optimize asset performance, extend equipment lifespan, and minimize downtime. By leveraging advanced features such as predictive maintenance, maintenance scheduling, analytics, integration, and recurring maintenance, manufacturers can achieve significant improvements in operational efficiency.
Predictive Maintenance
Transition from reactive to proactive maintenance, leveraging predictive analytics to identify potential issues before they lead to costly downtime. By implementing predictive maintenance strategies, you can optimize maintenance schedules and reduce unplanned breakdowns.
Maintenance Scheduling
Efficiently schedule maintenance tasks, minimizing disruptions and maximizing asset utilization. With an intuitive scheduling interface, you can allocate resources effectively, plan maintenance activities, and ensure that maintenance tasks are completed on time.
Analytics
Analyze data to optimize maintenance strategies and enhance overall productivity. By leveraging advanced analytics capabilities, you can gain valuable insights into asset performance, identify trends, and make data-driven decisions to improve maintenance efficiency.
Integration
Integrate with existing systems for seamless data flow and holistic asset management. By connecting your smart maintenance planner with IIoT, SCADA, OPCUA, ERP, and other on-prem systems, you can achieve a unified view of your shopfloor operations and optimize maintenance workflows.
Recurring Maintenance
Tailor the solution to fit your specific industry and facility requirements, ensuring maximum value. Whether it's scheduling routine maintenance tasks or managing complex maintenance processes, the smart maintenance planner can be customized to meet your unique needs.
Take the Next Leap: Embrace Proactive Maintenance and Revolutionize Shop Floor Efficiency
In conclusion, the power of smart maintenance planning cannot be overstated in today's competitive manufacturing landscape. By implementing a modern maintenance planner, you can shift from reactive to proactive maintenance practices, minimize unplanned downtimes, and optimize the performance of your assets. Features such as predictive maintenance, maintenance scheduling, analytics, integration, and recurring maintenance empower manufacturers to make smarter decisions, maximize uptime, and drive overall equipment effectiveness (OEE).
At IfElseCloud, we offer a comprehensive suite of solutions designed to transform your maintenance planning process. Our smart maintenance planner integrates seamlessly with your existing systems, provides real-time insights using machine learning and AI, and allows for efficient production board management, work order management, and reporting and insights. With our integrated shopfloor solution, you can achieve synchronized production and maintenance schedules, streamline data collection and analysis, and drive continuous improvement.
Don't let unexpected machine breakdowns hinder your productivity and profitability. Embrace the power of smart maintenance planning with IfElseCloud and take your manufacturing operations to new heights.
Contact us today to learn more about how our solutions can revolutionize your maintenance practices and unlock the full potential of your shopfloor.